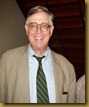
Friends of the Taconic State Park October 23, 2010
I’m delighted to be back at this wonderful park which, as you know, is one of the original State Parks in the Taconic Region, dating back to 1928. It marvelously combines all three elements that are proclaimed in the agency’s name: parks, recreation and historic preservation. To put it another way, you could adopt as the Friends’ motto one that I heard the other day on the radio: “history is in our nature.”
And indeed it is – for it was nature in the form of iron ore, water power and firewood that made the industrial history of this place, and it is nature in a much more nurturing manner that has been making it a beloved site of public recreation for campers, hikers and swimmers for over 80 years. This then-and-now, bifocal, history of Copake Falls and of the environs of romantic Bash Bish summons up the image beloved of students of American history: the “machine in the garden.”
I must tell you that personally I love this sort of synergy. For over 35 years, first at the Environmental Conservation Department and then at State Parks, I have espoused the convergence of culture and nature as one unified precious environment demanding our protection and enjoyment. It seems to me that you as a Friends group are very much on this same mission.
Even in these tough economic times the stewards of this park do a terrific job and I am happy to add my word of praise for all that Ray has done to foster Taconic State Park, to your good fortune (he is now promoted to Region-wide responsibilities but continues here as well); Garrett Jobson, who has efficiently advanced the plans for the splendid new building at the Ore Pit swimming area, and who also has now been given larger responsibilities; and it is great to see a Commission member here, Art Gellert, and a soon-to-be Commission member, carrying on a grand family tradition, your own Edgar Masters.
But these ARE tough times, and the stabilization plans for the historic furnace that Larry Gobrecht, Tom Schofield and others developed years ago have languished. They languish no longer! It is truly wonderful news that this iconic structure from the 1870’s will be getting a sheltering cover that will greatly slow its deterioration and assist in telling the story of industry in this place.
Make no mistake – it is an important story: the iron industry hereabouts was one of the earliest extractive and manufacturing enterprises in the country, dating back to the mid-18th century and Philip Livingston, Second Lord of the Manor. But what arose at Copake Falls in the 1840’s was a sophisticated, well-financed, state-of-the-art business that took advantage of the railroad and created what was a company town. A glance at the published maps or at the diorama leads us to explore for the remnants underfoot (such as the old narrow-gauge railbed) or in plain sight (Upjohn’s lovely Episcopal chapel). The remnants are here. Industrial archaeology is increasingly championed as an important element in our American heritage.
Here we are within the Hudson River Valley National Heritage Area, which celebrates the region as a “corridor of commerce” among other signal attributes. Yet we can point to remarkably few actively promoted, publicly accessible heritage sites associated with industry and commerce. You have one of the few right here, listed on the National Register of Historic Places in 2007, and the Greenway folks should be promoting it along with your efforts and those of State Parks.
Another nice then-and-now link is the fact that an important product of the company was iron ploughshares, many of which were put to work on neighboring lands such as the still-operating Langdonhurst Farms in this breadbasket valley now vitalized by C.S.A.s.
Fifty years ago Freeman Tilden came up with a credo that I think applies beautifully here at this park and this heritage site:
Through interpretation comes understanding;
Through understanding comes appreciation;
Through appreciation comes protection.
Viable iron mining and manufacturing may have departed our region for the Mesabi Range in Minnesota and elsewhere in the 1890’s, but we must nevertheless understand, appreciate and protect what remains from this heritage. Emphatically that is what this exciting project is about.
I am deeply impressed that a third of the estimated $150,000 cost is already committed as in-kind services – skilled labor, materials, use of equipment. This project is doable, and it is really important that it be done. I congratulate the Friends’ board, members and advisory committee on all that they have already achieved, and for receiving the 2010 Heritage Award from the Columbia County Historical Society for your commitment to this industrial heritage.
I relish the notion of families coming to camp, swim and hike in these beloved lands, and returning home with their imagination enhanced by visions of man’s long-ago very different use of these same resources. It is from such a bifocal vision that a true understanding and appreciation of nature and culture will emerge.
Our parks and historic sites have never needed their friends more surely than they do today in in this bleak and problematic political and fiscal climate. We must all be grateful that your Friends group is on the job. I wish you all success in this grand endeavor!
J. Winthrop Aldrich
(retired as New York State Deputy Commissioner for Historic Preservation on October 1, 2010)